Author |
Message |
   
John_vreede
| Posted on Thursday, August 02, 2018 - 06:03 am: |
|
Sorry if this is longer than most people are used to - its aimed at people who haven't cleaned their wiring loom earths/grounds - yet. Hopefully useful background info for those that have. The post applies to ALL Aluminium framed Buells but the particulars are given for a Uly (the only Buell I have access to is mine). Its needs additional info about where the grounds on Lightnings S and SS variants and Firebolts are and how many etc. Can an owner of each that knows pls post - jv A light throttle/low speed/moderate rpm cough or hiccup or misfire or stutter or pop, or whatever you want to call it, is a common problem on XB’s. A big part of the fix is cleaning up the earthing joints from the wiring loom. What is not discussed much is WHY the corrosion causes so much trouble, or HOW to fix it so it doesn’t come back again. WHY The basic reason the earth joints corrode is because aluminum is actually a very reactive metal. It only seems unreactive because its covered by a thin film of non-conductive oxide, which must be breached at any electrical joint. Where aluminum touches another metal with a different reactivity (like low reactivity copper, tin, lead or their alloys) in the presence of a bit of moisture, it sets up an electrolytic corrosion cell with its own small voltages, a bit like a thermocouple. Where 2 aluminum surfaces touch and are made to carry a current (like the earth return current from starter motor through the engine and frame), that also promotes corrosion when wet and/or salty. Using the frame to do double duty, carrying the earth return current as well its other functions, is the way Erik Buell designed the Buell. Electro-chemically, it’s just not a good idea. In airplanes it can’t be avoided; every ounce matters. They don’t run extra ground wires and don’t normally have corrosion problems, so there must be a way of doing it properly. An RNZAF Avionics Engineer told me earth wires must have a resistance of less than 0.7 Ohm, otherwise stray voltage drops can be set up, that affect control computers and other electronics. Steps on how to do it properly are in the HOW section below. The bit about ‘...stray voltage drops … that affect control computers…’ is important for the misfire/stutter/hiccups. The ECM reads voltage drops across the various sensors. Most sensors have their own earth return loops in the wiring harness, but 2 sensors do not; the Engine Temperature sensor and the O2 sensor. Both are earthed through the engine. If there are electrical joints that have high resistance (corroded) or if there are induced voltages, like you get in metal close to induction coils (e.g. the ignition coil mounting bracket), then the ECM reads not only the voltage drop across the sensor, but the additional drop across the dirty joints and/or any addition or subtraction of induced voltage. If this varies (as induced voltages do, or the resistance of dirty joints does when stressed by engine vibration, road bumps etc), then the ECM ‘sees’ the sensor voltage changing and compensates for it. IT'S THE ECM COMPENSATING FOR THESE VOLTAGE CHANGES THAT CAUSES THE MISFIRES, STUTTERS etc. I believe this is why people swear an earth wire to the ignition coil mount stops misfires, when in any normal electrical wiring sense there is no need for it, as discussed here: https://www.buellxb.com/forum/showthread.php?41712-Grounding-the-coil Also, electro-chemically, you should not rely on ANY current path through aluminum if you can avoid it. Pure aluminum is a very good conductor of electricity, but its alloys are not. That, plus joints that corrode, is why you shouldn’t run earth return currents through it. And there are a couple of dodgy joints. You need to disassemble the rear end of the bike to clean the joints between the subframe and the main frame ‘…back to bright metal’, and then they are not easy to protect from road spray. Also, the connection from the subframe to the battery negative cable is shrouded by the cadmium plated steel battery tray. You should remove the battery tray to clean that joint properly, but most people won’t. You can avoid all these issues by running a thick copper earth cable from the frame side of the braided earth strap, at the top anti-vibration mount above the engine, back to the battery negative terminal. Pic1 & Pic2 Note the two extra wires in the lug at the anti-vibration mount end in the RH picture above; one runs forward to the earth point on the steering head, and another shorter one, connects to the rear coil mounting bolt. This means all earth return currents from the rear cylinder head back to the battery are carried through copper wires and solder-covered copper or brass lugs, directly to the lead negative terminal. All these metals have similar reactivity, so no corrosion cells are set up. The earth return current from the lights, horn and instruments also flow through low reactivity joints and any induced voltage in the coil bracket is quashed. A short wire between the 2 bolted earth points in the left-hand side of the rear subframe as shown below, means other sundry earth return currents, are also routed through low reactivity joints. All these earth joints are still connected to aluminum, but don’t NEED the aluminum as a current path. If you were OCD about it, you’d run an earth return from both the Engine Temp and O2 sensors, but engine vibration would be a problem and the above works. However, if you suspect a dud ET or O2 sensor, maybe try earthing it directly before replacing it??? HOW The Airforce earth bonding method is as follows: • Clean all contact surfaces with Scotchbrite or ~240 grit sandpaper, back to bright metal. • Spray all contact surfaces with a cleaner/corrosion inhibitor that “…improves electrical properties”, like CRC 2.26. • Torque up the joint while the contact surfaces are still wet with the cleaner/corrosion inhibitor. • Clean off the exterior of the joint with contact cleaner (CRC Brakleen or carb cleaner works too) • Spray the joint with a waxy corrosion protectant like CRC CPC400, to stop water seeping in and corroding it again. ‘Clean all contact surfaces … back to bright metal’ (e.g. on the braided earth strap) means cleaning: • the engine and frame surfaces where the joints bolt up (at least on the engine side) • both sides of each end of the dog-bone link • the new earth cable lug • as well as both sides of each end of the braided strap itself. • A tap into the threaded holes and cleaning the underside of bolt heads and their threads and washers is not strictly necessary now, because the bolts and the frame or subframe don’t need to carry any current. Loctite on bolt threads won’t affect joint conductivity either. I’ve only found 5 earth joints in the standard wiring on a Ulysses: • Two bolted inside the rear cast subframe, • One at either end of the braided earth strap between the frame and cylinder head bridging the dog-bone anti-vibration mount above the engine, • One bolted to the front of the steering head. • Don’t know if other XB’s have more or less – can someone who knows comment pls Sizes & lengths of extra cable and wire for a Ulysses are: • Cable from braided strap to battery negative = 20 - 25mm2 cross section and 29” long (eye centre to eye centre). Check length on other XB’s (shorter frames and/or different subframes). • Wire to steering head earth bolt = at least 0.75mm2 cross section and 36” long + however much is in the connectors. • Wire to rear coil mounting bolt = at least 0.75mm2 cross section and 12” long + connectors. • Wire between subframe earth points = at least 0.75mm2 cross section and 6” long (eye to eye). Check on XB’s with different subframes. • The cable I used was a 20mm2 earth cable from a small-car wiring loom (free from a wrecker). It already had a brass lug crimped and soldered on, to bolt to the battery. I cut it to length and got an auto electrician to crimp and solder a lug on the other end. Crimp-on lug: • get one sized for the cable + 2 extra wires with as big a surface area around the 5/16” hole as you can. • get it soldered as well as crimped (belt and braces). • Heat-shrink a sleeve that has glue inside it, over all 3 wires, to strain-relieve the 2 smaller wires so they don’t break from vibration. Spraying CPC400: • use cardboard behind the joint to give room to allow the spray to get to the back of the joint and rags or paper to catch the overspray. Pic 4 • use a heat-gun/hair dryer between coats to flash off the solvent, to build up the film thickness. Moarant posted this https://www.buellxb.com/forum/showth...ng-(-3500-RPM), (and BadWeb) which shows that doing continuity testing didn't pick up that the earth to the ECM was bad. Through some inspired guesswork he figured the ECM earthing was the problem and added an extra earth wire spliced into the ECM earth leads and running directly to the battery, which cured his problem. There are 2 possible causes I can think of for this: 1. Since the bike is a Lightning and the ECM earths on the opposite side of the subframe to the battery, that the joint between the sub-frame halves was corroded - fix with a wire between the earth points like on my Uly, or 2.That the crimp on the earthing lug was bad. I measured the resistance of my earth wires from the black ECM plug back to the sub-frame lug and found 7 Ohms resistance, however my misfire was cured by the earth cable and the high resistance crimp didn't seem to be part of that problem. After measuring, I did spray that joint, including the crimp, with CRC2.26 and since then the resistance has been lower every time I've measured it. That could be my poor measuring technique, but might also be the effect of the CRC2.26. I got an electrician with a Fluke DMM to measure it again today and the the resistance is back to near zero (as it should be) - so I won't be changing that crimped lug - but will keep an eye on it. Whatever be aware that crimps can go bad over time if they weren't made right to start with and be a source of voltage drop, which could cause a misfire like it did for Moarant. You'll only pick them up by measuring their resistance with a sensitive DMM, not by continuity testing. My ‘07 Ulysses had an intermittent misfire that was 99% fixed by running the earth cable from the braided earth strap to the battery negative and cleaning/corrosion-inhibiting both ends of the braided earth strap joints and both battery terminals as above (the last 1% was fixed by richening the mixture). The extra earth wire to the ignition coil mounting bolt didn’t make any difference on my bike, but probably would have if I hadn’t put in the earth cable and cleaned all the joints. However, because it’s so important to quash stray voltages, which may even be between parts of the engine, I did it anyway. I believe you should too. In an ideal world, Buell’s stock earth wiring works. But, as many people have found, if the bike starts to misbehave you have to clean the earth connections; the method given will clean and protect the standard wiring loom connections properly. Probably, just applying the Airforce earth bonding process to the standard wiring earth points would be enough in most cases. However, that still won’t improve the joints between the subframe and main frame and may not be enough to suppress induced voltage effects on the Engine Temp and/or O2 sensors. The earth cable from the braided strap, and the earth wire from the coil mount, are effective for this - jv
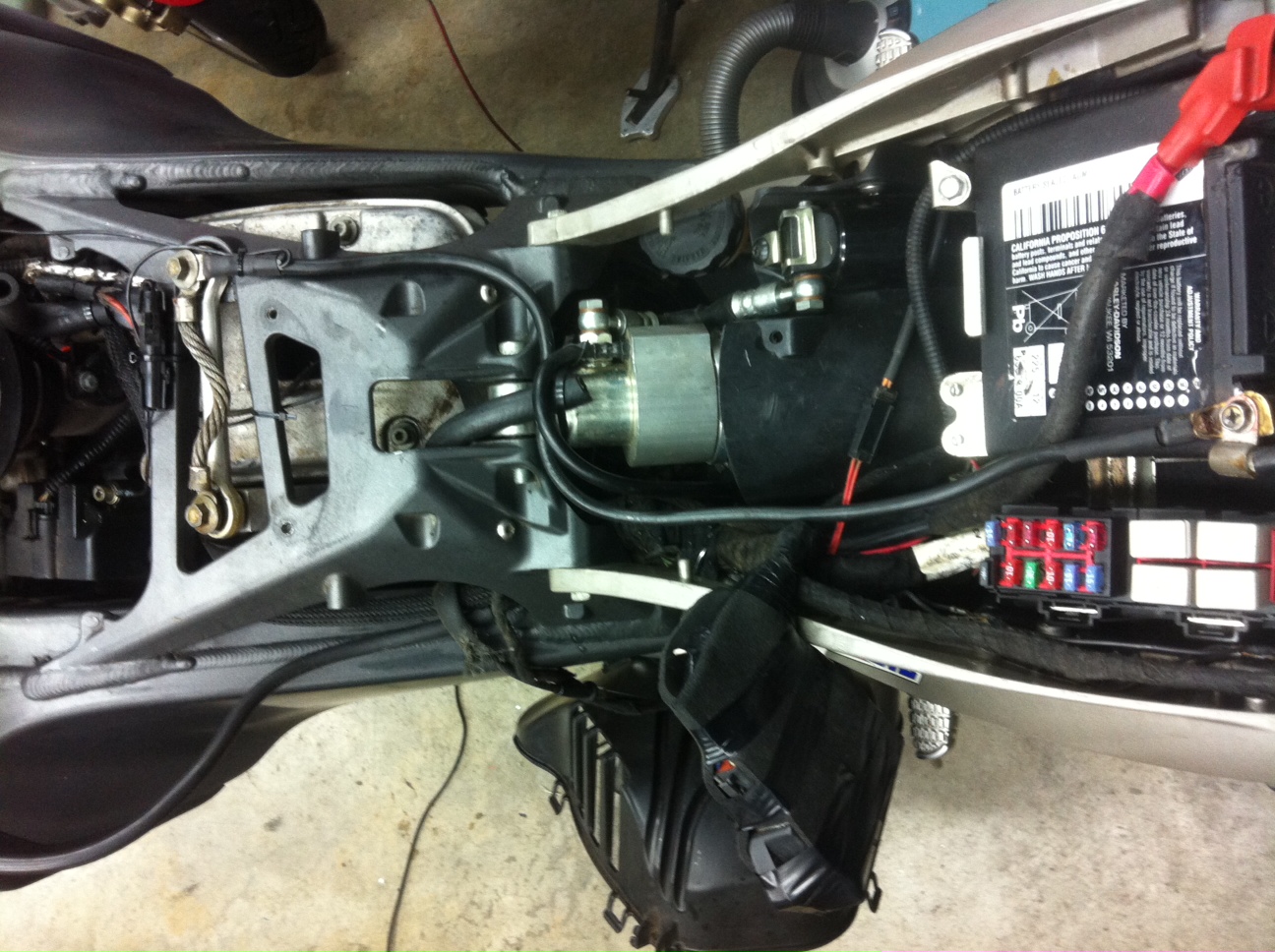
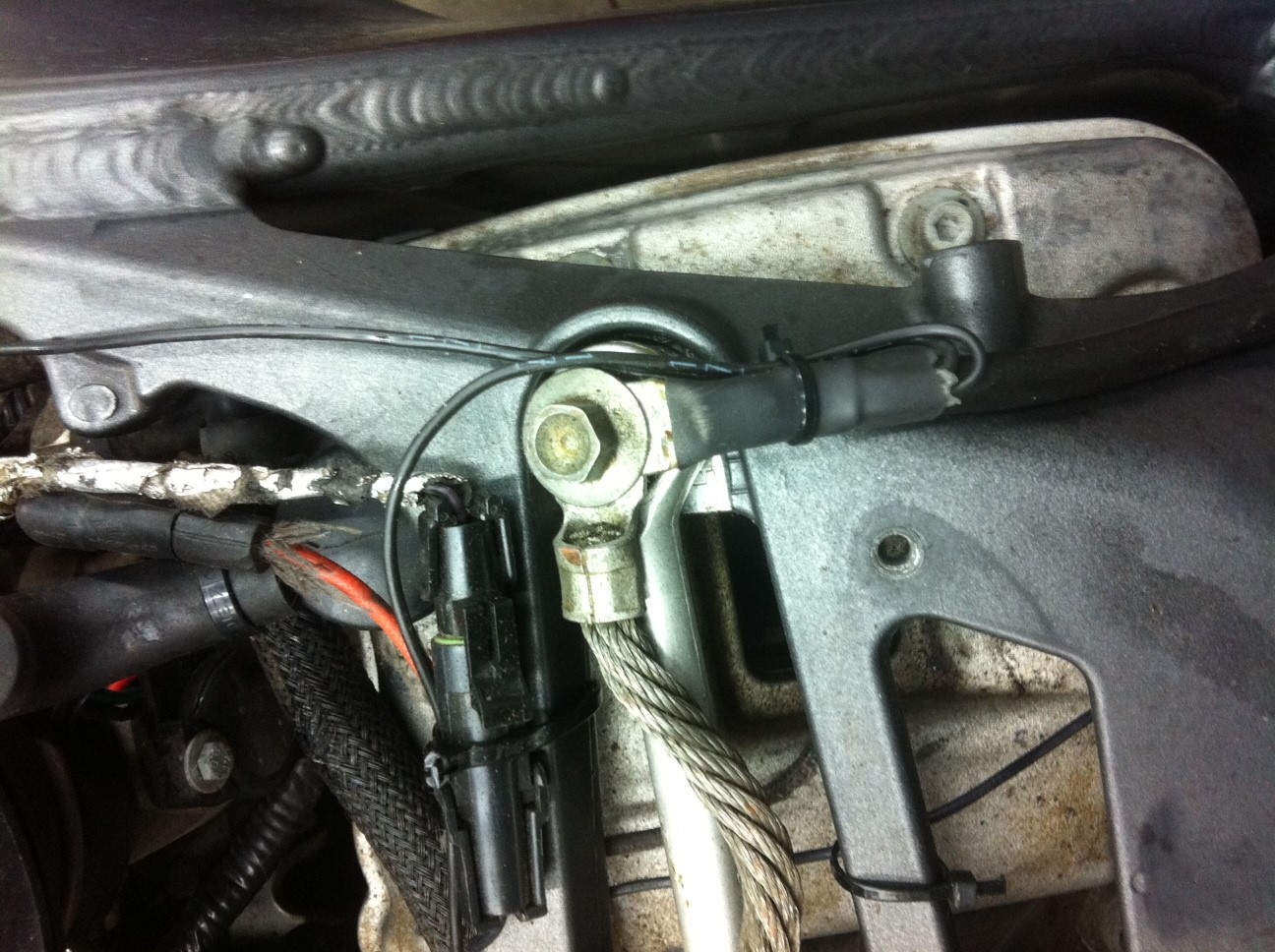

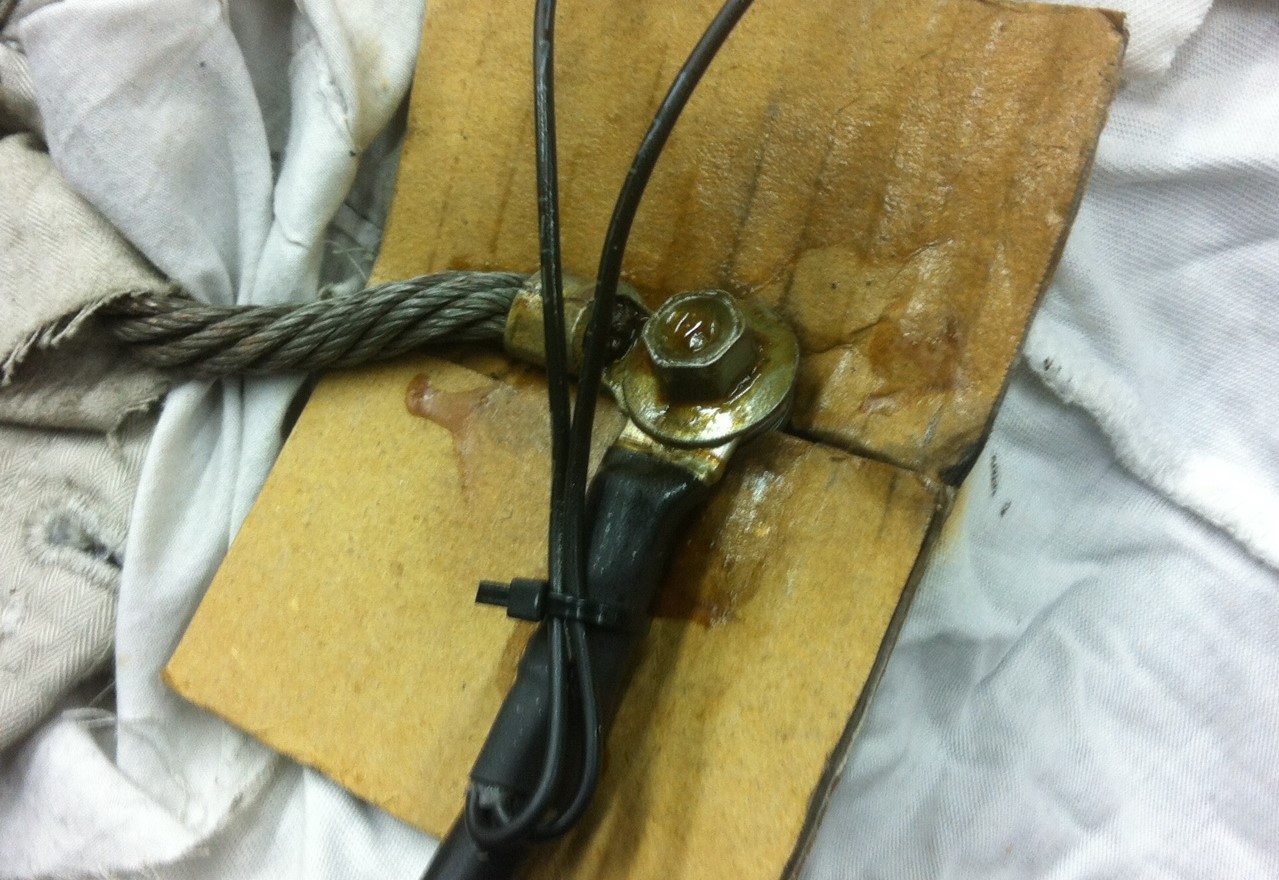
|
   
John_vreede
| Posted on Friday, August 17, 2018 - 01:08 am: |
|
Find attached a checklist that takes the stuff above and puts it on 2 pages that hopefully you can download - jv |
   
Mr_obsessive
| Posted on Sunday, August 26, 2018 - 11:34 pm: |
|
A BIG Thank-You for all your data research and pictures!! |
   
Tleighbell
| Posted on Saturday, September 01, 2018 - 09:13 am: |
|
I second that. |
   
John_vreede
| Posted on Saturday, September 01, 2018 - 08:33 pm: |
|
NASA and the military have produced documents and MIL-STD's about Galvanic corrosion of metals in electrical contact (which is what earth joint corrosion is). In an offline discussion, Gabby_duck from BadWeB showed me a NASA paper on electrical bonding (many thanks Alan!). It has a table showing which metals can be in contact with which, and what to do when they are. (see attached) The bullet points under the table are good background info - jv |
   
Greg_m
| Posted on Sunday, September 02, 2018 - 09:59 pm: |
|
Going through the ground connections has been on my list (along with fork seals, wheel bearings, etc. etc. ...) and I was hoping to make it to winter before tackling the project as my work schedule has left me next to no time at home this year. Sure I had to charge the battery more often than I thought reasonable, starting was often reluctant, sometimes the speedo would take time off, the check engine light came on once in a while etc.. But a trip to a local hardware store resulting in the need for a boost forced my hand. And there's only a million or so other chores that need immediate attention so I decided today would be the day. I followed the tutorial in the first post with only minor adjustments. The whole went smoothly. The bike is running great. The random pop when speed matching on deceleration is gone - I had assumed this had something to do with the inoperable exhaust actuator. Of course the new set of Iridium plugs I put in while I was at it can't hurt. I also put a volt meter where the accessory power outlet had been for good measure. I'm hoping a good bit of electrical weirdness has been exorcised.

|
   
2cylinderbill
| Posted on Sunday, December 02, 2018 - 11:27 pm: |
|
A big thank-you to JohnV from Bill in New Jersey. My wife and I took our 2008 Ulysses XB12X to Texas (COTA) in April. It got rained on heavily both at the track and extensively on the way there and the return trip. Previous to that, it had never seen rain since I bought it in 2012. Shortly after returning to NJ, it started to misfire, splutter and stall. It got to the point that it was nearly unrideable. Once I got a window of time where I could focus on it, I found and read the post above. It made perfect sense that after it endured all that moisture, that corrosion had begun to take hold at those ground connection points. Anyway, I created the thinner copper wires from #14 AWG and lugs picked up at Home Depot. For the connection from the anti-vibe mount back to the battery I bought these #2 AWG cables on Amazon. Total cost about $50. Worked like a dream and the bike is running like before April. I'm super happy so thanks again!! |
   
Gabby_duck
| Posted on Tuesday, December 04, 2018 - 07:44 am: |
|
Three biggest issues with the XB is 1) intake seals and 2) the above mentioned article. When doing intake seals it's hit or miss 3) is learning about AFV (adaptive fuel value.) YouTube and learn Fuel Trims to Better understand this. In my opinion ECM Droid is a must. Get the Buelltooth plug-in so you can see your AFV. Go to the Buelltooth web site it has great info (Message edited by Gabby duck on December 04, 2018) (Message edited by Gabby duck on December 04, 2018) |
   
Tpehak
| Posted on Monday, March 30, 2020 - 10:14 pm: |
|
IT'S THE ECM COMPENSATING FOR THESE VOLTAGE CHANGES THAT CAUSES THE MISFIRES, STUTTERS etc. I believe this is why people swear an earth wire to the ignition coil mount stops misfires, when in any normal electrical wiring sense there is no need for it, as discussed here: https://www.buellxb.com/forum/showthread.php?41712 -Grounding-the-coil Under any circumstances DO NOT PUT ADDITIONAL GROUND WIRE FROM BATTERY TO COIL OR TO ANY ANOTHER ENGINE PART!!! Why? Because of if the engine strut thick braided wire for some reason will have bad contact with frame or with engine or for some reason you will forgot to attach this strut wire back after disassembling the motorcycle you may burn you motorcycle because of when you press starter button all the battery current will go through your additional wire and if this wire is too long, or too thin, or has bad contact it will heat up and burn your motorcycle which may cause dead or serious injury. |
   
Blake
| Posted on Wednesday, April 01, 2020 - 12:46 pm: |
|
Or put a fuse in it.  |
   
Gabby_duck
| Posted on Wednesday, April 01, 2020 - 03:19 pm: |
|
Just keep your chassis grounds clean. Clean both the lugs and the aluminum frame with green scotch brite.Then I spray fluid film, Boesheild over the reattached hardware. This solved my trouble light issue of lean O2 sensor. Every now and then I have to redo this maintenance.my bike is a 09 ULY OEM |
   
Tpehak
| Posted on Wednesday, April 01, 2020 - 03:41 pm: |
|
If you have bad circuit from battery ground to engine case in first place the starter will not be able to crank the engine due to excessive resistance in this circuit. If the starter is able to crank the engine then all another component related to the engine case ground have just enough continuity on the battery ground to work properly. Adding extra wire between the battery negative terminal and engine case is dangerous and completely unnecessary. It may do the difference only if for some reason you have intermittent contact in the ground circuit and for some reason this circuit has good contact when motor does not work and bad contact when motorcycle is vibrating during engine is working. But like I said once that circuit will have bad connection you will burn your motorcycle once you hit the starter button and high current will flow through your additional inappropriate wire. So yes, if you feel you need additional wire do not do this. Instead of this clean and tighten negative battery terminal, battery to subframe ground, maybe subframe to frame contact spot, engine central strut braided wire both connections, maybe engine cylinders brace contact spots. This is the only appropriate thing you can do in this case. (Message edited by TPEHAK on April 01, 2020) |
   
Screamer
| Posted on Wednesday, April 01, 2020 - 08:24 pm: |
|
I’ve installed an additional cable (not wire) that is as large- or larger diameter, than the original battery cables. If all others grounds failed completely, the cable I’ve installed is large enough to handle the full amperage load of the starting cycle without fire risk. I agree that installing a small gauge wire as an additional ground may have some risk of overheating. I also agree that removing/cleaning/reinstalling is the correct way to address ground issues, but access to the grounds and the durability of copper to cast/forged aluminum joints (even after proper cleaning) is subject to fretting and corrosion - and the issue may return. Installing a large battery-to-tiebar ground cable however, may delay the frequency of the issue returning, and the required “cleaning the connections”. |
   
Tpehak
| Posted on Wednesday, April 01, 2020 - 09:49 pm: |
|
I heard some people route wire from the battery negative terminal to the ignition coil and attach it to the mounting screw of the ignition coil. That screw is not big and it goes to sheet metal part and makes not too big contact area with that part. So again if the battery ground to engine ground main circuit failed for some reason you also have risk of welding that tiny screw to the sheet metal bracket after you press starter button. |
|