Author |
Message |
   
Jolly
| Posted on Sunday, January 27, 2013 - 11:24 am: |
|
Ive designed a part that I think other riders will like. I have one prototype that I want to make subtle changes to but the CNC shop I was using seems to have too much going on and theyre not returning calls anymore. I would like the part copied with small changes, then a production capability. please PM me if you have the capability. This part clamps 1 1/8 handlebars into the Tube frame style bikes like X1 and S1 and retains the stock guage mount face and capability to mount the stock bikini fairing. This has been a long process that began with a want to be able to mount Ducati monster bars on my S1W, It has taken me almost a year..or longer to get this far and it is finally near finish! frustrating for something so simple to take so long!!! |
   
Greg_cifu
| Posted on Sunday, January 27, 2013 - 03:44 pm: |
|
Are you talking about a new upper triple clamp and top clamp replacement? *IF* you already had a 3D CAD model designed that a machine shop could use, that's going to run you $300-500 in small quantities. Then you'll have to mark it up for whatever you think your profit should be. If you're wanting somebody ELSE to reverse engineer your current parts, THEN make parts, I'd expect to pay $1000 or more for the first article and $300-500 for subsequent parts. Prices come down with quantities but, that's only possible because tooling has to be built to hold the parts in each position for machining. The same challenges will still hold true if you're thinking of some kind of adapter blocks to fit in the existing saddles. Costs will be lower than a whole triple but, will probably be higher than you think. |
   
Gmaan03
| Posted on Sunday, January 27, 2013 - 04:15 pm: |
|
Yes do you have good models to provide a shop with? We have some machine time available. If the parts are not to involved let me take a lookie. |
   
Jolly
| Posted on Sunday, January 27, 2013 - 04:27 pm: |
|
I have a good working model, its already been mocked up on the bike, just need one small change, I want to make the body of it a little thicker, can make a clay build up of the area I want thicker. will send a PM |
   
Jolly
| Posted on Sunday, January 27, 2013 - 04:28 pm: |
|
I have a good working model, its already been mocked up on the bike, just need one small change, I want to make the body of it a little thicker, can make a clay build up of the area I want thicker. will send a PM |
   
Greg_cifu
| Posted on Sunday, January 27, 2013 - 05:33 pm: |
|
No, no, you're not understanding: a clay model is worthless. If that's all you have, somebody still has to 3D scan it, then create surfaces, then create models, then cutter paths. Now you're into many thousands of dollars before you make the first part. You MUST have a three-dimensional Computer Aided Design (CAD) model or nobody can manufacture it on a CNC. You MIGHT be able to get a sand-cast of it made from your clay & aluminum model but, that will still require some post machining. That price will still shock you for fewer than 5-10 parts. |
   
Arizona_buell
| Posted on Sunday, January 27, 2013 - 05:58 pm: |
|
If you don't find what you are looking for send me a P.M. You only need 3d model If it is 3d machining you are looking for. I do prototype stuff all the time. Mark This is 3d machining 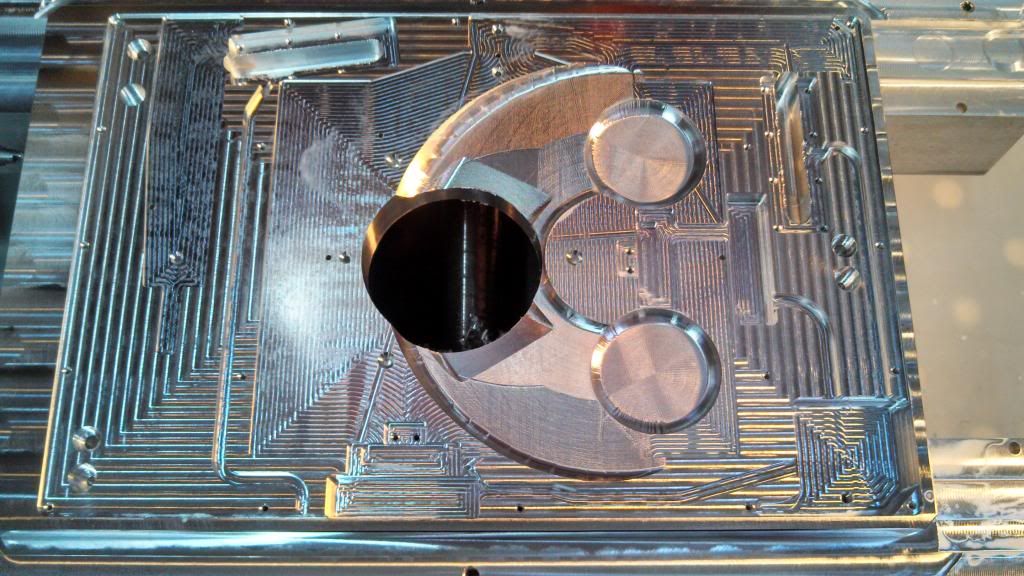 |
   
Jolly
| Posted on Sunday, January 27, 2013 - 06:26 pm: |
|
I have the part made, I just want a small change made to it to add some thickness to a flat plane area. I was a test pilot for a while in my "younger" days and I thought the engineers were trying to kill me, it would appear that they still are!  |
   
Loose1
| Posted on Sunday, January 27, 2013 - 10:19 pm: |
|
I might be able to help you out, depending on the quantity you are looking for and the timeline. I make vacuum formed molds for a living and I have a small home shop that I do stuff on the side. Mostly Buell parts or building custom parts for friends and families' old cars. Send me a pic of what you are wanting and the quantity you're look for and I'll see what I can do for you. I've got a 3 axis cnc mill with Mastercam and a smaller manual lathe. Matt |
   
Greg_cifu
| Posted on Sunday, January 27, 2013 - 10:25 pm: |
|
quote:I was a test pilot for a while in my "younger" days and I thought the engineers were trying to kill me, it would appear that they still are!
There are two kinds of test pilots: those who know that the engineers are leading them to water to save their life and the ones who insist we're trying to drown them.  |
   
Gmaan03
| Posted on Monday, January 28, 2013 - 12:10 am: |
|
@ arizona buell what software do you use? Nice looking work. I build molds and such too. |
   
Arizona_buell
| Posted on Monday, January 28, 2013 - 10:19 am: |
|
Feature Cam is what we are using. Not my choice just what we have. Works fine just takes some getting used too. Thanks for the compliment. Those things end up with wired out hinges and 3 sections float, some electronic B.S. Lot of work for a few parts but Oh well. Most of what I do here is for the Aerospace industry. |
   
Radon30
| Posted on Monday, January 28, 2013 - 10:40 am: |
|
How long does it take to machine a piece like that? I would think tool feed speed would have to be pretty slow. |
   
Greg_cifu
| Posted on Monday, January 28, 2013 - 12:14 pm: |
|
Feeds and speeds in aluminum are very fast. This will give you some idea: http://youtu.be/uc5P6Ss3LRE Total cutting time on something like a triple clamp might only be an hour or so, including some ball milling on contoured surfaces, etc. It would be greatly reduced in production but, that would take a five axis machine like in the video above. The problem is that there is a TON of programming time to make a part like a triple clamp. Most triple clamps have at least four setups and probably more depending on how many different angles the drill holes go. Every one of those requires either custom fixtures to position things in a known location or other features designed into the part to use as locating positions for subsequent operations. I know a guy who made a custom triple lower triple clamp. It was his own design and he had absolute control over which direction each drill hole went, etc. That damn thing still took him 30-40 hours between CAD time, programming, actually running it, multiple setups, one scrapped part, etc. The only fundamental change he was making was larger bores so he could use bigger fork legs than stock. |
   
Radon30
| Posted on Monday, January 28, 2013 - 12:40 pm: |
|
I meant the the part A.b. showed , its a very intricate part. It is amazing how fast a cnc machine can turn a block of steel or aluminum into an usable object. |
   
Thylacine
| Posted on Monday, January 28, 2013 - 02:55 pm: |
|
this is what I'm working on right now. I can help you. it is probably not worthwhile to have me write the code for it, if it is only a few pieces I could just turn them out manually.

|
   
Arizona_buell
| Posted on Monday, January 28, 2013 - 07:12 pm: |
|
The 3d portion of the plate I showed took about 16 min. Finish on the flow part of the large radius was not super critical. Finish is everything with 3d milling. The finer the finish the more step overs you need to create that finish with a ball mill. The code for this part would fill many pages if you printed it out. The side shown took about two hours total including a slew of 0-80 tapped holes. The most time was the tolerances on some of the pockets. I don't really need the work I am working 65 plus hours a week already. I was just offering if it was needed. If the O.P. needs help or wants help I can help. Here is one of the flywheels we make for a Porsche engine,aftermarket lightened setup. And here are some double Caliper mounts for a motorcycle shop.
And a piston fixture for a large motor company to mill valve relief.
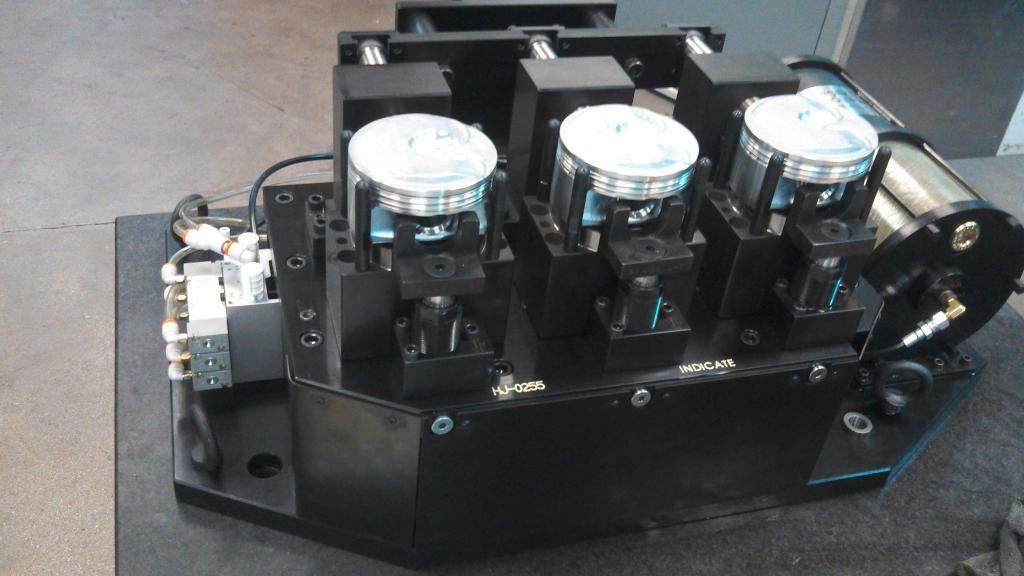 |
   
Jolly
| Posted on Monday, January 28, 2013 - 11:38 pm: |
|
Thanks thylacine, gmaan03 reached put so I sent him a few photos of what I currently have to see if he thinks he can help. It's nothing complicated, I believe, and not a full triple tree. I drew up a part that would allow me to use 1 1/8 bars on a stock top clamp and still use stock gauge mount, its been made as a prototype and mocks up to correct fitment. Somehow the "company" that made the first one for me is simply to busy to make changes and they do have a lot going on. I'm also looking for a more finished product. Let me see what gmaan03 comes up with before I reach out to someone else. Thanks! |
   
Gmaan03
| Posted on Tuesday, January 29, 2013 - 09:11 am: |
|
That is some nice stuff you guys made. Currently I am using Master Cam to program a five axis to cut carbon fibre parts. I would love to post a couple pics, but can not, our company is very strict about this. I just made four billet shifters for my X1 ill post up a pic when complete. I modified the fulcrum points so the shifting is much easier. |
   
Kc_zombie
| Posted on Tuesday, January 29, 2013 - 11:21 am: |
|
Here is a picture of the block of wood I am working on. Can't seem to get that edge right...
 I feel dumb... Just kidding! (Message edited by kc_zombie on January 29, 2013) |
   
Purpony
| Posted on Tuesday, January 28, 2014 - 11:02 pm: |
|
i know this is a year old, but did you ever get this worked out Jolly? (Message edited by purpony on January 28, 2014) |
|